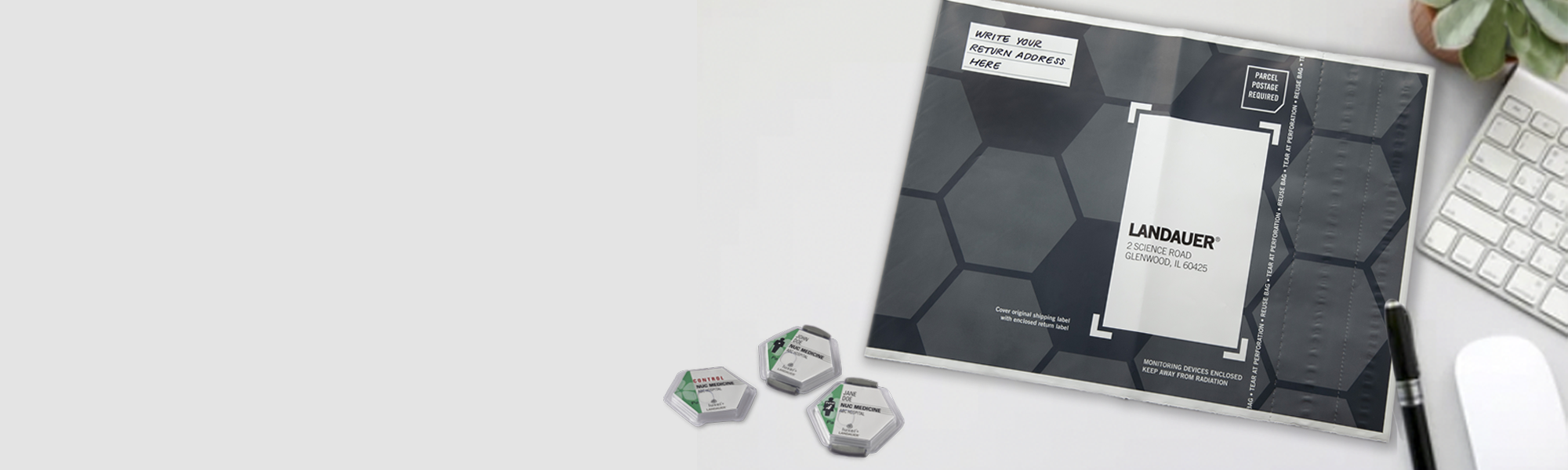
Exchanging Dosimeters: When, Why, and How
You may view the dosimeter exchange process to be a management challenge. Collecting everyone’s badges, adding the control badge that comes with each shipment, sending in the package, and then distributing the new badges to start the next wear period can be confusing if a routine system isn’t in place.
Yet did you know that the dosimeter exchange process actually forms the foundation of your practice’s radiation safety program? And that you are a very important part of the process? Read on to find out more…
How Often Should Dosimeters Be Exchanged?
The length of time you wear your dosimeter before returning it is called the wear period. This wear period is the catalyst behind the whole dosimeter exchange process, and it is unique to your practice.
What determines your wear period?
- The type of ionizing radiation equipment you’re using
- The length of time for a typical procedure
- The average number of procedures you conduct in a week
- The average number of procedures an employee conducts per week
- Your ALARA program guidelines
Essentially, if your techs are not exposed to very much radiation at all, the wear period will be longer. And conversely, if they are working in a high-exposure environment, the wear period will be shorter. The most common wear periods are one month, two months, and three months.
Why Exchange Dosimeters?
The dosimeter exchange process is set up so that you can monitor your team’s doses on a regular basis.
When you reach the end of your wear period, you need to give your employees a new set of dosimeters and send the worn ones back to us so we can analyze them and generate your reports. This ensures you remain in compliance with your state and/or federal regulations.
What Do We Do with the Dosimeters After They’re Returned?
Once the worn dosimeter badges are returned to LANDAUER, we analyze them in our lab. We are an accredited dosimeter processor of the National Voluntary Laboratory Accreditation Program (NVLAP Lab Code 100518-0) for ionizing radiation dosimetry. Each dosimeter badge has a serial number associated with the participant/employee for permanent traceability of the radiation dose data.
Luxel+ dosimeter badges are analyzed using an optically stimulating luminescence process, special to LANDAUER, resulting in a precise and accurate radiation dose reading. Because of the analysis methodology that allows for test repeatability, if a question or concern regarding the dose reading arises in the future, the badge can be re-read and a discussion with the technical team can take place.
What Do the Dosimetry Reports Say?
Each badge reading generates a LANDAUER Radiation Dosimetry Report, which clearly outlines the occupational dose measurements for each participant.
This report, which will be uploaded to your myLDR portal within 10 business days after analysis, is the legal dose of record. Each report contains a wide range of data for review by radiation safety leaders giving detailed information needed to ensure a quality and compliant program required by federal, state, and local agencies.
The report also tracks each badge wearer’s cumulative radiation dose throughout the year so that you can monitor how close your employee’s dose is to the annual ALARA (As Low As Reasonably Achievable) radiation dose limit.
Want to learn how to read the report? Check out this helpful video.
How to Read Your Report from LANDAUER® on Vimeo.
Other reports may be generated at different checkpoints throughout the year or upon request, depending on your account setup.
The Dosimeter Exchange Process Checklist
“Depending on the size of your practice, keeping track of everyone’s dosimeter badge can be tricky. Yet with a standard approach, this important job should become an easy, routine task in no time,” says Linda Vrabec, Senior Customer Success Manager at LANDAUER.
Here are some tips for setting up a routine system for your practice from the LANDAUER team:
- Keep track of everyone who wears a badge. They should all be listed in your myLDR account.
Click to download Keep your account up to date. Make updates anytime staffing changes occur, or to order fetal badges for declared workers and/or spare badges for spot needs.
- Make sure your staff knows that they must remove the tab before clipping the Luxel+ badge into the plastic holder. Here’s a short video demonstrating the technique.
- Keep your control dosimeters – those that come with each shipment to monitor ambient radiation in the transportation and storage process – away from the employee badges, and be sure to include them in your return shipments.
- When the wear period is complete, gather up all of the used and unused dosimeters (including area monitors!) at the end of each wear period, along with the control dosimeter(s) of the same type and wear date.
- Package the badges up for shipment. You can use our preprinted labels that are included, or if you want to use your own labels, make sure you use a trackable shipping method and ensure there is enough postage applied. Postal delays will occur for shipments that do not have enough postage, causing your processing and reporting to be delayed as well.
Watch this video to learn how to do a smooth exchange.